Steps to Better UPS Budgeting
1. Get proactive: The first step is understanding that proactive UPS maintenance is not optional; it’s essential to both developing a budget and preventing budget blowout due to unexpected equipment failure. Consider the cost of a run-until-failure approach with fans, as one example. Heat sinks can form and quickly destroy equipment, such as SCRs, IGBTs and power modules. Letting a single IGBT be destroyed by heat can cost upwards of $1,200 – all preventable by regular fan replacement.
Proactive parts replacement also helps equipment run more efficiently for lower utility bills and added savings. How do you stay on track? It’s easy! Your dedicated DC Group account manager is here to help you every step of the way.
2. Get the right tools for the job: D-Tech™ is part of DC Group’s proprietary PowerTools Suite™. This software is complimentary with your maintenance contract – it helps you do your job, and it helps us do ours. In fact, the PowerTools Suite is key to DC Group’s 100% service completion rate and lightning-fast on-site response time during an emergency.
D-Tech has everything you need to keep track of your UPS maintenance – including billing information, upcoming appointments and detailed information on equipment and all UPS components. The “Proactive Replacement” screen lets you plan for each component (as well as replacement of entire UPS units) 10 years into the future! D-Tech has a full-function app for mobile power management. See a full demo video of D-Tech here.
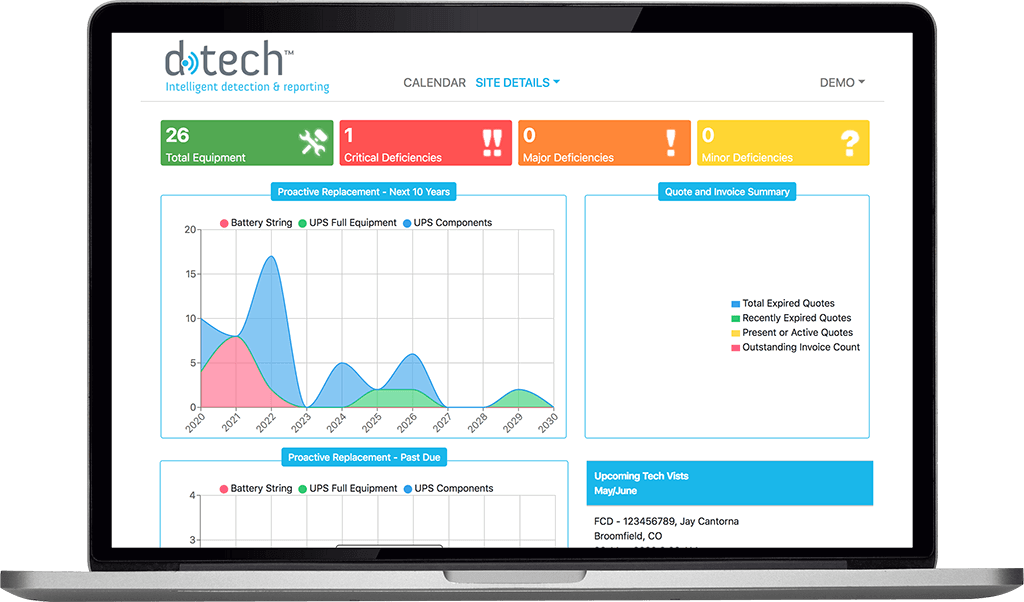
D-Tech Proactive Replacement
D-Tech is unique in the industry in that it’s an interactive, searchable and actionable database that’s accessed at three points: by you (the client), by your account manager, and by your DC Group engineer. This means information is uploaded on the spot during a site visit, and communication is immediate and always up-to-date.
3. The power of parts! DC Group is an independent maintenance provider, which means we support all makes and models. It also means we support original equipment past the point where the OEM may have discontinued support, so you can make the most of your original UPS budget. How do we do this? We developed the single largest inventory of UPS parts in the industry – including OEM-discontinued and rare parts. We maintain every make and model of UPS unit built since the 1980s, and we keep it all going strong so you can replace when it makes sense for your budget vs. when the unit is no longer supported.
Here’s a recent example: A client was moving operations to a new facility. The construction company quoted him $100,000 for a new 10kVA unit. DC Group instead moved his current UPS (30kVA) and did a battery/capacitor/fan refresh – all for under $10K. This client saved 90% and ended up with a larger unit with tons of life left in it.
4. Go with the pros! Proactive budget planning includes an understanding of where an organization is headed, as well as its priorities for continuous operations. Is the business experiencing growth that will put a higher demand on UPS units? Is the organization planning on expanding and installing more UPS units? How resilient must the operation of the mission-critical system be, and what does the organization consider a fast response? An experienced account manager knows how to ask the right questions so your service is seamless and your planning is rock-solid for years to come.
At the same time, our experienced UPS engineers make sure service is done right the first time. We never subcontract; all service is performed by full engineer-employees who have a minimum of 5 years OEM or military UPS experience, and who receive ongoing training on all units at our state-of-the-art training facility.
Experience, insight, a massive parts inventory and our independent/expert service all add up. Get in touch to find out more about smarter power planning for your UPS budget!